Superhydrophobic surfaces, generally characterized by a water contact angle (CA) over 150°, exist extensively in nature, for example the surface of lotus leaves and water-strider legs. Creating artificial superhydrophobic surfaces and exploring their versatile applications, such as waterproofing, selfcleaning, drag reduction, and selective absorption, have become exciting research frontiers. However, good stability, flexibility, practicability, and universality of superhydrophobic coatings are needed for practical use, and multifunctionality has been a new focus of superhydrophobic coatings. Nonetheless, superhydrophobic smart coatings for wearable sensing applications have not yet been reported.
Recently, ZHANG Ting’s group in the Suzhou Institute of Nano-Tech and Nano-Bionics (SINANO), Chinese Academy of Sciences, reported a novel superhydrophobic and piezoresistive coating with high flexibility and universal applicability to various substrate materials. Related results were published in Advanced Materials under the title “A Superhydrophobic Smart Coating for Flexible and Wearable Sensing Electronics”, and the article was selected as the inside cover paper.
In this work, a highly flexible multifunctional smart coating is fabricated by spray-coating multiwalled carbon nanotubes dispersed in a thermoplastic elastomer solution, followed by treatment with ethanol. The coatings not only endow various substrate materials with superhydrophobic surfaces, but can also respond to stretching, bending, and torsion—a property useful for flexible sensor applications. The coatings show superior sensitivity (gauge factor of 5.4–80), high resolution (1° of bending), a fast response time (<8 ms), a stable response over 5000 stretching–relaxing cycles, and wide sensing ranges (stretching: over 76%, bending: 0°–140°, torsion: 0–350 rad m-1). Moreover, multifunctional coatings with thicknesses of only 1 μm can be directly applied to clothing for full-range and real-time detection of human motions, which also show extreme repellency to water, acid, and alkali, which helps the sensors to work under wet and corrosive conditions.
This work is supported by the National Natural Science Foundation of China (61574163), the Science Foundation for Distinguished Young Scholars of Jiangsu Province.
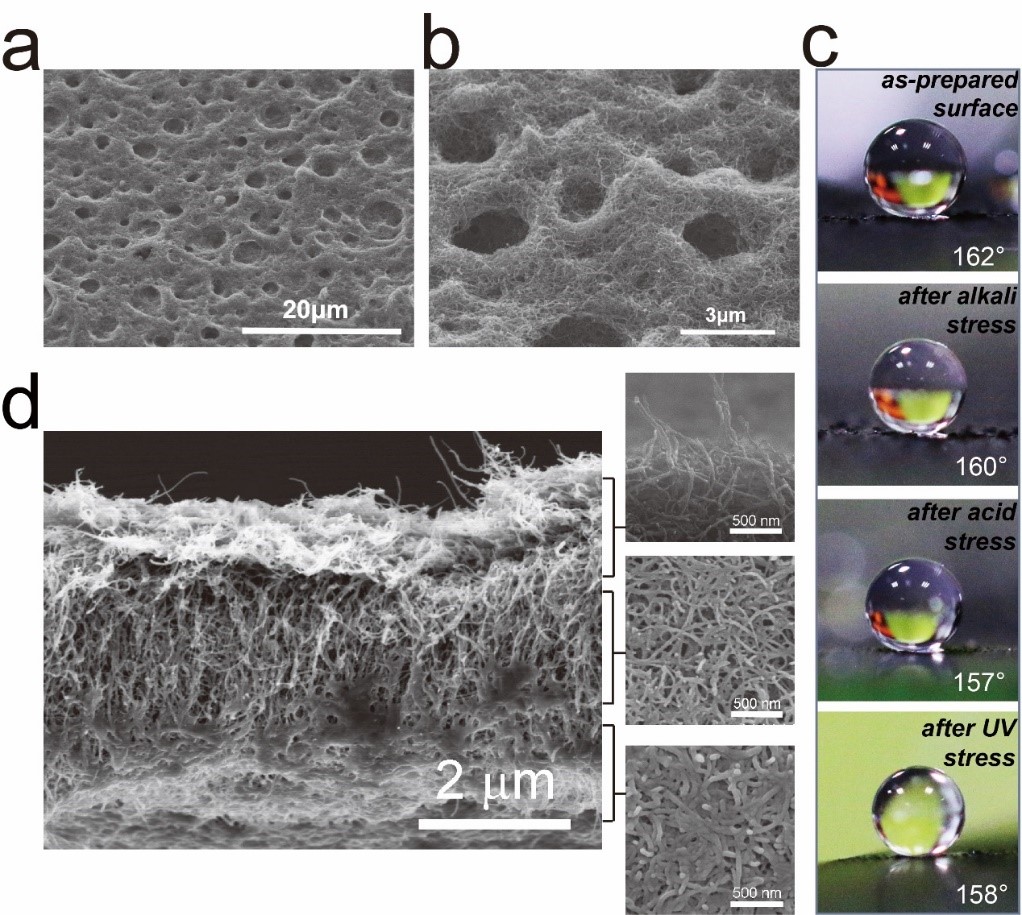
Figure1. (a) (b) SEM images of the MWCNT/TPE-film surfaces, (c) Optical photographs showing the contact angles of water droplets (≈3 μL) on coated glass substrates as-prepared and after different treatments. (d) SEM image showing the cross-sectional micromorphology of MWCNT/TPE composite film treated with ethanol for 2 min.(Image by SINANO)
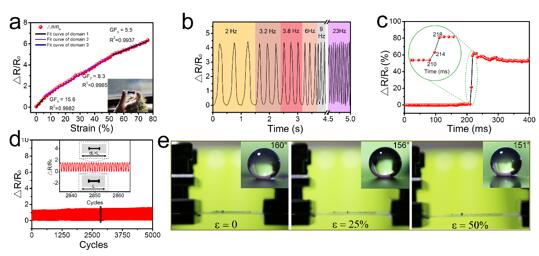
Figure2. (a) Normalized relative resistance as a function of tensile strain and the linear fittings. Inset: Optical photograph of the sensor. b) Real-time variation in the resistance under repetitive stretching from ε = 0% to ε = 50% with different frequencies. c) Time response of the sensor upon applying a quasitransient step strain from ε = 0% to ε = 5%. Inset: Enlarged figure showing the response time. d) Normalized relative resistance variation under cyclic stretching from ε = 0% to ε = 10% with a frequency of 0.5 Hz over 5000 cycles, which shows the reproducibility and durability of the sensor. e) Optical photographs of water droplets (≈3 μL) on the MWCNT/TPE film with different tensile strains. Insets: Enlarged photographs showing the water contact angles. (Image by SINANO)
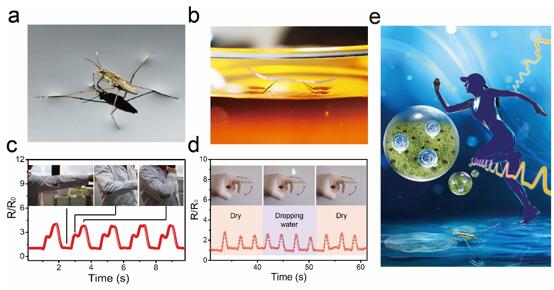
Figure3 (a) (b) Optical photograph of real strider and a strider-like copper robot on water, with the four “feet” of the robot coated with magnetic MWCNT/Fe3O4/TPE films. In the experiments, colored pigment was added into the water for better observation. (c) Real-time variation of the normalized relative resistance. Insets: Optical photographs showing the bending movement of the elbow joint wearing coated lab gown. (d) Normalized relative resistance as a function of time. Insets: Schematics showing the repetitive bending of the index finger wearing a coated glove under discontinuous water dropping. (e) Inside cover picture.(Image by SINANO)
Contact information:
Links: Website of ZHANG Ting’s group : http://nanosensor.sinano.ac.cn/
Literature: http://onlinelibrary.wiley.com/doi/10.1002/adma.201770310/full