Flexible and wearable bionics-sensors, as the most exciting frontier in the field of flexible electronics, have attracted more and more attention due to their unique properties (attachable, wearable, and foldable) and potential applications in consumer electronics, homeland security, and health-related equipment etc. Microstructured polydimethylsiloxane (PDMS) film is considered to be the most popular flexible substrate to integrate sensitive nanomaterials for the flexible sensors due to its excellent elasticity and biocompatibility. However, the current fabrication method for patterned PDMS is complicated and expensive, requiring multi-steps (spin coating, lithography, and etching etc.). The large area integration with nanomaterial assemblies is also less reproducible.
Recently, professor Ting Zhang and colleagues from the Suzhou Institute of Nanotech and Nanobionics (SINANO), Chinese Academy of Sciences (CAS), developed a simple and low-cost method for the fabrication of large-area patterned PDMS conducting thin films with uniform microstructured patterns. The researchers found the high-quality textiles such as silk with microstructured surface intertextures are effective moulds for construction of wearable and flexible PDMS thin films. Meanwhile, combining silk-molded micro-patterned PDMS and SWNTs ultrathin film (reported previously Journal of Materials Chemistry, 2012, 22, 21824-21827), they demonstrate a new type of flexible artificial bionics-sensors with superior sensitivity (1.8 kPa-1), lowest detectable pressure limit (0.6 Pa), fast response time (10 ms), and highest stability (>67500) for detection of super slight pressures. The result was published on the current issue of Advanced Materials, 2014, 26, 1336-1342, and was highlight in the Front Cover. This work may open a novel and facile method for developing nanomaterials-based flexible nanoelectronics sensing devices, and also may broaden their potential use as cost-effective wearable electronics for prevention of illnesses and prediction of early disease.
The authors acknowledge the funding support from the National Natural Science Foundation of China, and the Hong Kong, Macao and Taiwan Science & Technology Cooperation Program of China. Also, they thank technique support from Printable Electronics Research Center of SINANO, CAS.
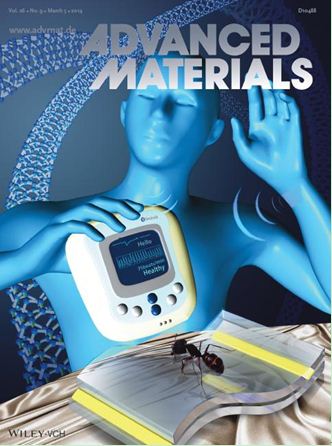